Whether it’s a medium-sized machine builder or a global player – Pilz supports companies worldwide with a comprehensive services portfolio. In an interview, Jürgen Bukowski, Global Services Consulting Senior Manager, Pilz GmbH & Co. KG, presents the component “Consulting”.
Mr Bukowski, what are the duties of the worldwide consulting group?
The consulting group is part of Global Services. Our team has three main tasks. Centrally, we look after the development of consulting services for the Pilz Group worldwide. Then we have around 400 service engineers in our 42 national subsidiaries who take care of implementation.
Secondly, our team advises Pilz’s global customers, for example, branded goods manufacturers with over a hundred production sites worldwide. They want machinery that is safe and complies with the standards and legal requirements – and not just in one country. Global players like these want an internationally consistent approach, whether that be technical specifications, procedures or training of employees.
And finally, we coordinate the work of the Pilz service hubs established worldwide. These deliver consulting services to countries where we don’t have our own sales and service company.
Consulting is part of Pilz’s services portfolio. What is the connection to the other services?
Consulting is embedded in our services portfolio for the whole machine lifecycle. When companies contact us, at first it is usually a matter of defining corporate standards. Companies need an insight into the jungle of requirements and directives. Initially we help to establish their own standards, in order to have a common understanding.
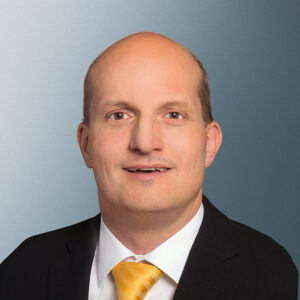
“This way we manage to always stay one step ahead and can support our customers at an early stage.”
Jürgen Bukowski, Global Services Consulting Senior Manager
This is followed by training and specific specialist training, to bring all employees up to the same level of knowledge. Then we advise customers and analyse machinery safety tasks that they are unable to resolve themselves. Our engineering service is available if any defects are identified or optimisations are required.
Which consulting services does Pilz offer specifically?
I’d like to highlight the consulting offers “Machinery Safety Evaluation” and “Machinery Acceptance”. With Machinery Safety Evaluation the task is to scrutinise existing machinery – when a company takes over an existing production site, for example. The available fleet of machinery must be inspected for defects and for compliance with legal and corporate standards. The state machinery can be in constantly surprises you.
The second task is Machinery Acceptance. All machines that are purchased from new must meet the specifications, of course, and have an EC declaration of conformity, for example. In this case we are often already on site at the machine builder’s. That’s because it is easier to rectify any defects there, than when the machinery is already built into the production plant.
In future the issue of security will also play an important role. How are you dealing with this?
In the field of safety we can assume defined protection goals and work with established classifications and probabilities. That makes our work easier.
“And finally, we are in a position to support companies of all sizes to the same level of quality across the world, over the whole machine lifecycle.”
Jürgen Bukowski, Global Services Consulting Senior Manager
Dealing with security is more difficult because protection goals can vary. Some machines or processes are more critical than others, and require more protection. With security, companies can determine what they want to protect. That makes dealing with security more complex. In this case it is even more important for companies to define their requirements and protection goals at the start. Here too, our special Industrial Security services provide support with a Protection Requirements Analysis, as well as a more extensive Risk Analysis to examine and increase cybersecurity. By the way, Industrial Security will be an important component of the EC Declaration of Conformity once the EU Machinery Regulation applies from January 2027.
How does Pilz manage to deliver services worldwide to the same quality?
We continually monitor what is happening worldwide in the field of machinery safety. We work closely with the Pilz Standards Group, which deals with standards for Pilz worldwide and actively participates in many standards and standardisation committees. We process the innovations or changes and prepare internal training and white papers to share the information with national subsidiaries. They, in turn, are experts on national specifications and know the local particularities.
We use a worldwide, uniform methodology and standardised processes for internal knowledge transfer. Our global services process is certified to ISO 9001. This way we manage to always stay one step ahead and can support our customers at an early stage.
How does our consulting offer benefit our customers?
Customers can be certain that, with Pilz, they are always on the safe side. We relieve them of the burden involved in guaranteeing safe, compliant machinery. Many of our consultants are also trainers, and vice-versa. This means that we can approach our tasks with a high degree of practical relevance. And finally, we are in a position to support companies of all sizes to the same level of quality across the world, over the whole machine lifecycle. I think that’s unique in scope and quality.