Presses have a special status when it comes to safety requirements. Grass GmbH, global manufacturer of movement systems for furniture and household appliances, was aware of this while looking for a partner that would be able to update “slightly” older plants to the current state of the art in compliance with standards. In Pilz Austria, the Salzburg-based company found a partner who could “complete the job in textbook fashion.”
“Functional movement” for furniture means more at the Grass Group than just “open and close”. Every application requires the perfect movement solution. Following this approach, the Austrian global player has proven its innovative strength over the last 75 years, including with the first trolley guide or the world’s first double-walled drawer system. “With around 1 900 employees at 21 locations and more than 200 distribution partners in 60 countries, we are the largest provider for movement systems,” states Andreas Huber.
He is the Maintenance Manager in Grass’s Salzburg factory. “With our machinery, we mainly bring plastics into the desired form, but thanks to two press lines we also do the same with stainless steel products for household appliances,” he explains. The latter is performed at “seasoned” older-model plants that were completely modernised and brought to the state of the art with regard to safety and control under the lead of Pilz Austria.

Partner for standard-compliant solutions
The first round of retrofits with Pilz took place back in 2017. The reason was the relocation of an eccentric press from Höchst, the head office in the Vorarlberg state, to Salzburg. “It had to be linked to an existing profiling plant and an upstream reel. This inspired us to look for a provider to not only replace the control technology of the automatic punching press, but to also perform a close inspection of the entire production line, assess this with regard to compliance with standards, perform the necessary adaptations and last but not least check the function of the higher-level safety concept,” clarifies the Maintenance Manager, regarding a task that other automation providers with whom he placed inquiries would not even consider.
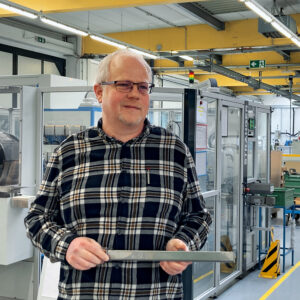
“Through these two press projects our collaboration intensified immensely. We now communicate with each other regularly. Should a similar conversion become necessary, we know exactly who to turn to based on our previous experiences.”
Andreas Huber, Maintenance Manager, Salzburg plant, at Grass
One reason for this is the fact that presses are listed in Annex IV of the Machinery Directive in the category of machines that require a separate conformity assessment procedure due to their dangerous characteristics. “As we brought our first press safety controller onto the market in 1995, Pilz is able to rely on more than 25 years of experience in this sector. We are in close contact with our colleagues from the expert team at the headquarters in Ostfildern committed solely to conversions and new installations of press controllers, particularly for projects such as at Grass,” explains Ronald Kahr, Sales Engineer at Pilz Austria. During a second retrofit in 2021, there was no question that the general overhaul of a press for the Salzburg plant should once again be carried out with Pilz experts.
Safety-related complete solution for high-end production
“The task consisted of exchanging the old controller in order to increase the process stability during forming of low to high-alloy steels,” summarises Thomas Stellberger, Manager of the Grass factory in Salzburg. As part of this, the existing contactor control as well as the safety circuit of the entire press line were updated. They were replaced by the configurable Pilz small controller PNOZmulti 2 with special modules and certified software blocks for a safe activation of presses. For the standard automation, the higher-level automation system PSS 4000 from Pilz was integrated.
Maintenance Manager Andreas Huber goes into detail: “This upgrade project involves a double-sided eccentric press for progressive dies, year of construction 1987, in which telescopic slides for ovens receive the corresponding punch-outs, imprints and inscriptions. Aspects to be considered with regard to safety and control included the upstream feed of the endless belt via a reel as well as the connected profiling machine.” Additionally, the problem of a feed that was already defective was also to be solved with the retrofit.
Upgrade to and around the press
Pilz took over all the tasks as part of the safety service, from the risk assessment to the creation of the safety concept and on to the validation and CE marking. The retrofit of the entire press line – comprising the three machine parts reel with straightener, profiling machine and automatic punching press – included installation of a completely new switch cabinet and control console as well as the wiring of all new safety-related components. The safety technology upgrade of the profiling machine additionally included the integration of the safe small controller PNOZmulti 2, together with new rope pull switches and the coded safety switch PSENcode for position monitoring.
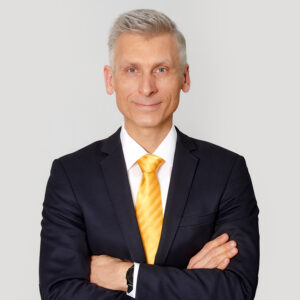
“Pilz can draw on more than 25 years of experience in the field of press safety control.”
Ronald Kahr, Sales Engineer at Pilz Austria
Pilz also kept an eye on the plant section reel with straightener: Today this is protected by the safety locking device PSENmlock for safe interlocking and guard locking, which can be easily managed via the control unit PITgatebox. And wherever barrier-free safety had to be retrofitted via light curtains, the safety light curtains PSENopt II for finger, hand and body protection from Pilz supplement the light curtains already installed. Following the conversion, Grass received a press line that was ready for production.
The Maintenance Manager at the Salzburg Grass factory sums it up with high praise: “Pilz products were already in use before, but through these two press projects our collaboration intensified immensely. Keeping to the deadline, manufacturer-neutral advice, the actual implementation and the final conformity assessment procedure – everything really worked perfectly.”